ඉන්ජෙක්ෂන් මෝල්ඩින් යනු විවිධාකාර ප්ලාස්ටික් කොටස් සහ නිෂ්පාදන නිෂ්පාදනය කිරීම සඳහා බහුලව භාවිතා වන නිෂ්පාදන ක්රියාවලියකි.මෙම බහුකාර්ය සහ කාර්යක්ෂම ක්රියාවලිය මගින් සංකීර්ණ හැඩතල සහ සංකීර්ණ කොටස් ඉහළ නිරවද්යතාවයකින් සහ පුනරාවර්තන හැකියාවෙන් මහා පරිමාණයෙන් නිෂ්පාදනය කිරීමට හැකියාව ලැබේ.ඉන්ජෙක්ෂන් මෝල්ඩින් ක්රියාවලිය පියවර කිහිපයකින් සමන්විත වන අතර, ඒ සෑම එකක්ම උසස් තත්ත්වයේ කොටස් නිෂ්පාදනය සහතික කිරීම සඳහා තීරණාත්මක වේ.ඉන්ජෙක්ෂන් මෝල්ඩින් ක්රියාවලිය පියවරෙන් පියවර ගවේෂණය කරමු.
පියවර 1: එන්නත් අච්චු නිර්මාණය
එන්නත් අච්චු ගැසීමේ පළමු පියවර වන්නේ අච්චුව නිර්මාණය කිරීමයි.අච්චු නිර්මාණය ප්රශස්ත කොටසේ ගුණාත්මකභාවය සහ නිෂ්පාදනය සහතික කිරීම සඳහා කෙටුම්පත් කෝණය, බිත්ති ඝණත්වය ඒකාකාරිත්වය, ගේට්ටුව සහ ඉෙජක්ටර් පින් ස්ථාන සහ සිසිලන නාලිකා ස්ථානගත කිරීම වැනි සාධක සලකා බැලිය යුතුය.අවසාන කොටසෙහි මාන නිරවද්යතාවය, මතුපිට නිමාව සහ ව්යුහාත්මක අඛණ්ඩතාව නිර්ණය කිරීමේදී අච්චු නිර්මාණය ඉතා වැදගත් වේ.අච්චු නිර්මාණය අවසන් වූ පසු, එය නිරවද්ය යන්ත්රෝපකරණ ක්රියාවලීන් භාවිතයෙන් නිෂ්පාදනය කෙරේ.
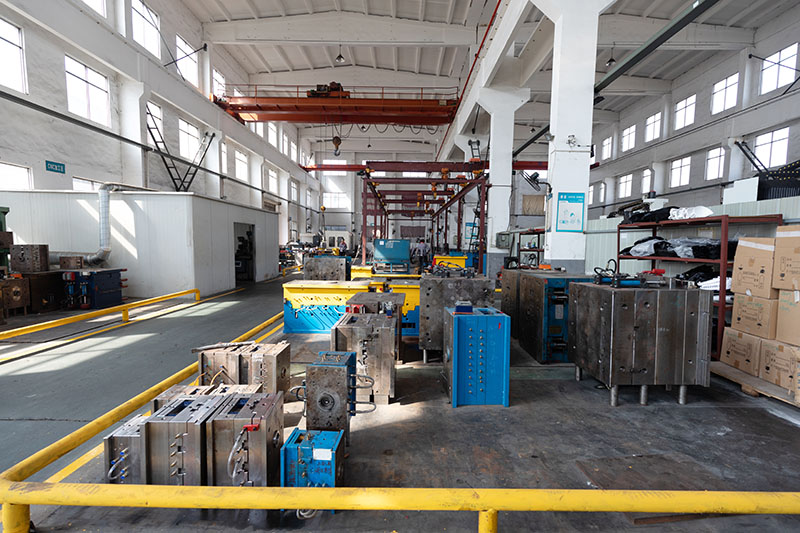
පියවර 2: ද්රව්ය සකස් කිරීම
අමුද්රව්ය, සාමාන්යයෙන් පෙති හෝ කැටිති ආකාරයෙන්, අවසාන නිෂ්පාදනයේ නිශ්චිත අවශ්යතා මත පදනම්ව ප්රවේශමෙන් තෝරා ගනු ලැබේ.නිමි කොටස අපේක්ෂිත ගුණාංග ඇති බව සහතික කිරීම සඳහා ද්රවාංක ප්රවාහය, දුස්ස්රාවීතාව, හැකිලීම සහ ශක්තිය වැනි ද්රව්යමය ගුණාංග සලකා බැලීම වැදගත් වේ.අතිරේකව, අපේක්ෂිත කාර්ය සාධනය සහ පෙනුම ලබා ගැනීම සඳහා මෙම අදියරේදී ද්රව්ය මිශ්රණයට වර්ණක, ආකලන හෝ ශක්තිමත් කිරීමේ තන්තු ඇතුළත් කළ හැකිය.
පියවර 3: කලම්ප සහ එන්නත් කිරීම
ද්රව්ය සහ අච්චුව සකස් කළ පසු, ක්රියාවලියේ කලම්ප සහ එන්නත් කිරීමේ අදියර ආරම්භ වේ.සංවෘත කුහරයක් සෑදීම සඳහා අච්චුවේ කොටස් දෙක එන්නත් අච්චු යන්ත්රය තුළ ආරක්ෂිතව එකට ගැට ගසා ඇත.එවිට ප්ලාස්ටික් ෙරසින් නිශ්චිත උෂ්ණත්වයකට රත් කර ඉහළ පීඩනයක් යටතේ අච්චුව තුළට එන්නත් කරනු ලැබේ.උණු කළ ද්රව්ය කුහරය පුරවන විට, එය අච්චු වින්යාසයේ හැඩය ගනී.එන්නත් කිරීමේ අදියර සඳහා එන්නත් කිරීමේ වේගය, පීඩනය සහ සිසිලන කාලය වැනි ක්රියාවලි පරාමිතීන් ප්රවේශමෙන් පාලනය කිරීම අවශ්ය වන අතර එමඟින් හිස් තැන්, සින්ක් ලකුණු හෝ විකෘති වීම වැනි දෝෂ වළක්වා ගත යුතුය.
පියවර 4: සිසිලනය සහ ඝන වීම
කුහරය පුරවා ගත් පසු, උණු කළ ප්ලාස්ටික් අච්චුව ඇතුළත සිසිල් කර ඝන විය හැක.අවශ්ය කොටස් කාර්ය සාධනය සාක්ෂාත් කර ගැනීම සහ චක්ර කාලය අවම කිරීම සඳහා නිසි සිසිලනය ඉතා වැදගත් වේ.අච්චු සැලසුමෙහි සිසිලන නාලිකා ඇතුළත් වන අතර එමඟින් ද්රව්ය ඉක්මනින් හා ඒකාකාරව තාපය විසුරුවා හැරීමට උපකාරී වන අතර ස්ථාවර කොටසක ගුණාත්මකභාවය සහ මාන ස්ථායිතාව සහතික කරයි.නිමි භාණ්ඩයේ අඛණ්ඩතාවයට හානි කළ හැකි කොටස් විරූපණය හෝ අභ්යන්තර ආතතිය වැනි ගැටළු වළක්වා ගැනීම සඳහා සිසිලන ක්රියාවලිය අධීක්ෂණය කිරීම සහ ප්රශස්ත කිරීම ඉතා වැදගත් වේ.
පියවර 5: පිටකිරීම සහ කොටස්
ඉවත් කිරීම ප්ලාස්ටික් සම්පූර්ණයෙන්ම සිසිල් වී ඝන වීමෙන් පසුව, අච්චුව විවෘත කර ඇති අතර අලුතින් සාදන ලද කොටස කුහරයෙන් පිට කරනු ලැබේ.අච්චුව තුළට ගොඩනගා ඇති ඉෙජක්ටර් පින් එකක් හෝ යාන්ත්රණයක් සක්රිය කිරීමෙන් කොටස පිටතට තල්ලු කරයි, එය මෙවලම් මතුපිටින් මුදා හරිනු ලැබේ.විශේෂයෙන් සංකීර්ණ ජ්යාමිතිය හෝ තුනී බිත්ති සහිත කොටස් සමඟ කොටස හෝ අච්චුව හානි වැළැක්වීම සඳහා පිටකිරීමේ ක්රියාවලිය ප්රවේශමෙන් සලකා බැලිය යුතුය.කොටස් ඉවත් කිරීම සහ ඉවත් කිරීම වේගවත් කිරීම සඳහා ස්වයංක්රීය පද්ධති ක්රියාත්මක කළ හැකි අතර, සමස්ත නිෂ්පාදන කාර්යක්ෂමතාව වැඩි දියුණු කිරීමට උපකාරී වේ.
පියවර 6: කපා අවසන් කරන්න
කොටස ඉවත් කළ පසු, අතිරික්ත ද්රව්ය (බර්ර්ස් ලෙස හැඳින්වේ) කපා හෝ කොටසෙන් ඉවත් කරනු ලැබේ.මෙය අවසන් කොටස් පිරිවිතරයන් සාක්ෂාත් කර ගැනීම සඳහා අවශ්ය ද්රව්ය ඉවත් කිරීම, ගේට්ටු ඉවත් කිරීම හෝ වෙනත් ඕනෑම නිම කිරීමේ ක්රියාවලියක් වැනි ද්විතියික මෙහෙයුම් ඇතුළත් විය හැකිය.ඕනෑම මතුපිට අඩුපාඩු හෝ නොගැලපීම් ආමන්ත්රණය කරනු ලබන අතර, යෙදුම් අවශ්යතා මත පදනම්ව, කොටසට යන්ත්රෝපකරණ, වෙල්ඩින් හෝ එකලස් කිරීම වැනි අමතර සැකසුම් ලැබිය හැකිය.
පියවර 7: තත්ත්ව පාලනය සහ පරීක්ෂා කිරීම
ඉන්ජෙක්ෂන් මෝල්ඩින් ක්රියාවලිය පුරාවටම, උසස් තත්ත්වයේ කොටස් නිෂ්පාදනය සහතික කිරීම සඳහා තත්ත්ව පාලන පියවරයන් ක්රියාත්මක වේ.ක්රියාවලි පරාමිතීන් නිරීක්ෂණය කිරීම සහ පාලනය කිරීම, දෝෂ සඳහා කොටස් පරීක්ෂා කිරීම සහ මාන නිරවද්යතාවය, ශක්තිය සහ අනෙකුත් ගුණාංග තක්සේරු කිරීම සඳහා විවිධ පරීක්ෂණ පැවැත්වීම මෙයට ඇතුළත් විය හැකිය.
සාරාංශයක් ලෙස, ඉන්ජෙක්ෂන් මෝල්ඩින් ක්රියාවලිය සංකීර්ණ සහ බහුකාර්ය නිෂ්පාදන තාක්ෂණයක් වන අතර එය පුළුල් පරාසයක ප්ලාස්ටික් කොටස් සහ නිෂ්පාදන සුවිශේෂී නිරවද්යතාවයකින් හා කාර්යක්ෂමතාවයකින් නිෂ්පාදනය කළ හැකිය.ද්රව්ය සැකසීමේ සහ අච්චු නිර්මාණයේ සිට සිසිලනය, පිටකිරීම් සහ තත්ත්ව පාලනය දක්වා ක්රියාවලියේ සෑම පියවරකදීම, ප්රශස්ත ප්රතිඵල ලබා ගැනීම සඳහා විස්තර සහ ප්රවීණත්වය පිළිබඳ ප්රවේශමෙන් අවධානය යොමු කිරීම අවශ්ය වේ.ඉන්ජෙක්ෂන් මෝල්ඩින් ක්රියාවලියේ සෑම අදියරක්ම අවබෝධ කර ගැනීම සහ ප්රශස්ත කිරීම මගින්, විවිධ කර්මාන්ත සහ යෙදුම්වල අවශ්යතා සපුරාලීම සඳහා නිෂ්පාදකයින්ට උසස් තත්ත්වයේ, ලාභදායී කොටස් අඛණ්ඩව ලබා දිය හැකිය.
පසු කාලය: දෙසැම්බර්-12-2023