Thermoplastic elastomers (TPEs) are popular across industries for their unique combination of properties, such as flexibility, elasticity and weather resistance. These materials are widely used in applications that require the elastic properties of rubber and the ease of processing of thermoplastics.
One of the most common methods of processing TPE into finished parts is injection molding. In this article, we’ll dive into the intricacies of TPE injection molding, covering its process, benefits, challenges, and applications.
• Learn about TPE and its properties
Before delving into the details of TPE injection molding, it is important to understand the properties of thermoplastic elastomers. TPE is a class of materials that combines the properties of both thermoplastics and elastomers. They can be easily molded and formed using traditional thermoplastic processing techniques while still possessing the elastic properties of rubber.
TPE is a block copolymer composed of hard segments and soft segments. Hard segments contribute to strength and thermal stability, while soft segments provide flexibility and elasticity.
The popularity of TPE in injection molding applications is due to the following factors: Versatility: TPE offers a wide range of hardness and flexibility, making it suitable for a variety of applications.
Easy to process: TPE can be processed using standard injection molding equipment, allowing for cost-effective production.
Excellent elastic recovery: TPE can withstand significant deformation and return to its original shape, making it ideal for applications requiring elasticity.
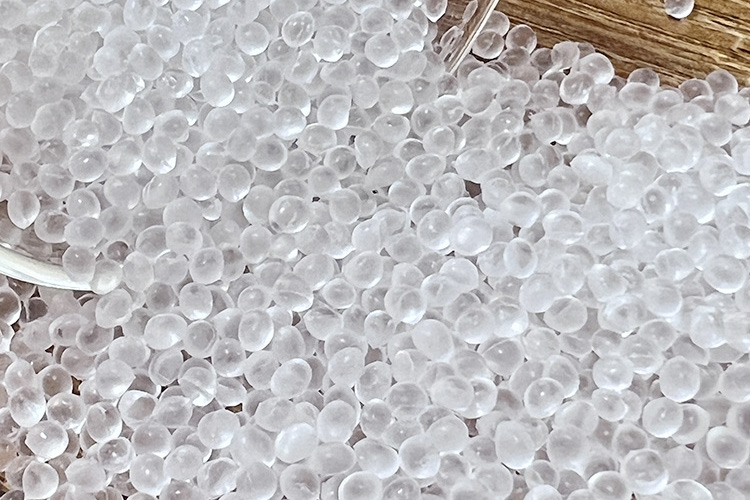
• TPE injection molding process
The injection molding process of TPE has similarities to the traditional thermoplastic injection molding process. However, for optimal results, certain considerations unique to TPE need to be addressed.
Material Handling: TPE is sensitive to moisture and proper material handling and storage is critical to prevent degradation and ensure consistent processing. Before processing, TPE pellets should be dried to the recommended moisture content to avoid problems such as surface defects and reduced mechanical properties.
Mold design and tooling: Mold and tooling design are critical to successful TPE injection molding. The mold should be able to provide uniform pressure and temperature distribution to ensure the production of consistent quality parts. Additionally, mold design should incorporate features such as draft angles, vents, and gates to optimize material flow and part ejection.
Process Parameters: Injection molding process parameters, including injection pressure, temperature and hold time, should be carefully optimized for the specific TPE material being processed. Proper understanding of the material's rheological behavior and processing characteristics is critical to achieving optimal part quality.
Injection Molding Machine: TPE can be processed using standard injection molding machines equipped with the necessary controls to handle the unique properties of the material. The settings of the injection device, mold clamping device and temperature control system should be adapted to the specific requirements of TPE processing.
• Advantages of TPE injection molding
TPE injection molding offers several advantages compared to other molding processes, especially when producing parts that require elasticity and flexibility.
Design Flexibility: TPE injection molding can produce complex geometries and intricate details, allowing for the design of innovative and ergonomic products.
Cost-effective production: TPE can be processed at lower temperatures and shorter cycle times than traditional elastomers, resulting in cost savings and increased manufacturing efficiency.
Material efficiency: TPE injection molding contributes to sustainability and environmental responsibility by minimizing material waste and enabling the production of lightweight, high-performance parts.
Overmolding capabilities: TPE can be easily overmolded onto substrates, allowing the creation of multi-material assemblies with enhanced functionality and aesthetics.
• Challenges and considerations
While TPE injection molding offers many advantages, it also presents some challenges that need to be addressed to ensure successful production.
Material selection: There are many different TPE formulations available, so material properties such as hardness, chemical resistance and UV stability need to be carefully considered to meet specific application requirements.
Mold Maintenance: TPE processing may result in increased mold wear due to the abrasive nature of the material. Regular maintenance and proper surface preparation are critical to extending mold life and maintaining part quality.
Processing Consistency: TPE injection molding requires precise control and monitoring of process parameters to ensure consistent part quality and minimize variations in material properties.
Adhesion to Substrate: When overmolding TPE to a substrate, adhesive compatibility and surface preparation are critical to ensuring strong bond strength and part integrity.
• TPE injection molding applications
TPE injection molding is widely used in a variety of industries including automotive, consumer goods, medical devices and electronics. Some common applications include:
Automotive seals and gaskets: TPE is used to produce flexible seals and gaskets that provide superior performance for automotive applications such as door seals, weatherstripping and HVAC components.
Soft-touch grips and handles: TPE injection molding is used to create soft, tactile grips and handles for tools, appliances and electronic equipment, improving user comfort and ergonomics.
Medical device components: TPE is used to manufacture medical device components such as tubing, connectors and seals, where biocompatibility, flexibility and sterilization resistance are critical.
Sporting Goods: TPE is used in the production of sporting goods, including grips, footwear components and protective equipment due to its cushioning, impact resistance and weather resistance.
• In conclusion
TPE injection molding offers a versatile and cost-effective solution for producing elastomeric parts with a wide range of properties and applications. As the demand for flexible, durable and functional products continues to grow, TPE is expected to play a key role in meeting the changing needs of various industries. Through careful material selection, process optimization and design considerations, TPE injection molding can bring new possibilities for innovative product development and enhanced performance.
Post time: Jan-04-2024