Injection moulding is a widely used manufacturing process used to produce a variety of plastic parts and products. This versatile and efficient process enables mass production of complex shapes and complex parts with high precision and repeatability. The injection molding process consists of several steps, each crucial in ensuring the production of high-quality parts. Let's explore the injection moulding process step by step.
Step 1: Injection mould design
The first step in injection moulding is designing the mould. Mould design must consider factors such as draft angle, wall thickness uniformity, gate and ejector pin locations, and cooling channel placement to ensure optimal part quality and manufacturability. Mould design is critical in determining the dimensional accuracy, surface finish, and structural integrity of the final part. Once the mould design is finalized, it is manufactured using precision machining processes.
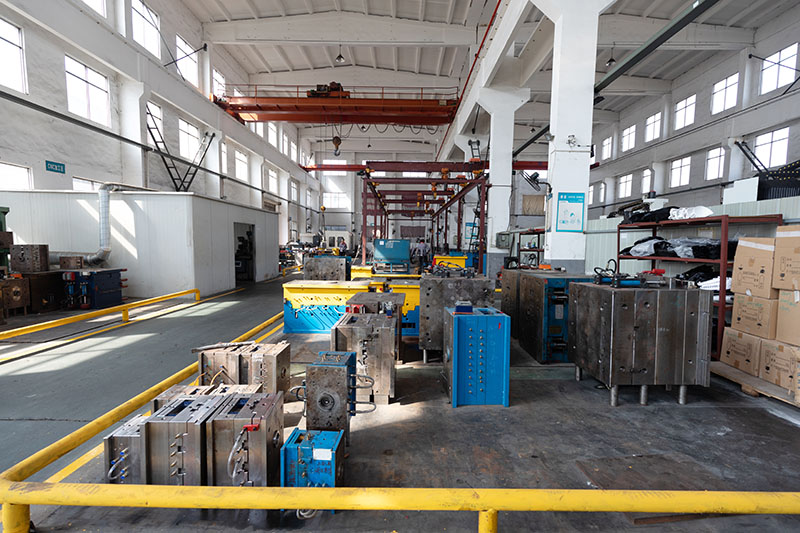
Step 2: Material Preparation
The raw materials, usually in the form of pellets or granules, are carefully selected based on the specific requirements of the final product. It is important to consider material properties such as melt flow, viscosity, shrinkage and strength to ensure the finished part has the desired properties. Additionally, colorants, additives or reinforcing fibers can be incorporated into the material blend at this stage to achieve the desired performance and appearance.
Step 3: Clamping and Injection
Once the material and mould are prepared, the clamping and injection stages of the process begin. The two halves of the mould are clamped securely together inside the injection moulding machine to form a closed cavity. The plastic resin is then heated to a precise temperature and injected into the mould under high pressure. As the molten material fills the cavity, it takes on the shape of the mould configuration. The injection stage requires careful control of process parameters such as injection speed, pressure and cooling time to avoid defects such as voids, sink marks or warping.
Step 4: Cooling and solidification
Once the cavity is filled, the molten plastic can cool and solidify inside the mould. Proper cooling is critical to achieving required part performance and minimizing cycle times. The mould design incorporates cooling channels that help the material dissipate heat quickly and evenly, ensuring consistent part quality and dimensional stability. Monitoring and optimizing the cooling process is critical to preventing problems such as part deformation or internal stresses that can compromise the integrity of the finished product.
Step 5: Ejection and Parts
Removal After the plastic has fully cooled and solidified, the mould is opened and the newly formed part is ejected from the cavity. Activating an ejector pin or mechanism built into the mould pushes the part out, releasing it from the tool surface. The ejection process must be carefully considered to prevent damage to the part or mold, especially with complex geometries or thin-walled parts. Automated systems can be implemented to speed up the ejection and removal of parts, helping to improve overall production efficiency.
Step 6: Trim and Finish
Once the part is ejected, any excess material (called burrs) is trimmed or removed from the part. This may involve secondary operations such as deburring, gate removal, or any other finishing process required to achieve final part specifications. Any surface imperfections or inconsistencies are addressed, and depending on application requirements, the part may receive additional processing such as machining, welding, or assembly.
Step 7: Quality Control and Testing
Throughout the injection moulding process, quality control measures are implemented to ensure the production of high-quality parts. This may include monitoring and controlling process parameters, inspecting the parts for defects, and conducting various tests to assess dimensional accuracy, strength, and other properties.
In summary, the injection moulding process is a complex and versatile manufacturing technology capable of producing a wide range of plastic parts and products with exceptional precision and efficiency. Every step in the process, from material preparation and mould design to cooling, ejection and quality control, requires careful attention to detail and expertise to achieve optimal results. By understanding and optimizing every stage of the injection moulding process, manufacturers can consistently deliver high-quality, cost-effective parts to meet the needs of diverse industries and applications.
Post time: Dec-12-2023