As an important innovation in the field of new energy vehicles, the integrated design of chassis and body is gradually changing the manufacturing method and performance of automobiles. The importance of mold technology as the core support for such integrated design is self-evident.
The development level of mold technology directly determines the manufacturing quality, efficiency and cost of key structural components of new energy vehicles, which in turn affects the development process of the whole new energy vehicle industry.
In this paper, we will discuss in depth the current status and application of mold technology for key structural parts of new energy vehicle chassis and body integration.
1. The importance of the integration of chassis and body of new energy vehicles
The emergence of the chassis and body integration design concept of new energy vehicles is not accidental, but in response to the development of the automotive industry in many ways. With the pursuit of environmental protection and energy efficiency, reducing vehicle weight has become one of the key factors in improving the energy efficiency of new energy vehicles.
By integrating multiple components into a single whole, the key structural components of chassis and body integration can significantly reduce the mass of the vehicle, thereby reducing energy consumption and improving range. For example, the overall weight of the vehicle can be reduced by a certain percentage after adopting the integrated design, which is of great significance in enhancing the market competitiveness of new energy vehicles.
In addition, the integrated design improves vehicle manoeuvrability and safety. The integrated structural components make the body stronger and the vehicle more stable during driving, enabling it to better cope with various road and driving conditions. In terms of safety, the integrated structure disperses collision energy more effectively and provides more reliable protection for passengers. For example, in the event of a collision, the integrity of the integrated chassis and body structure can be better maintained, reducing the impact on the occupants.
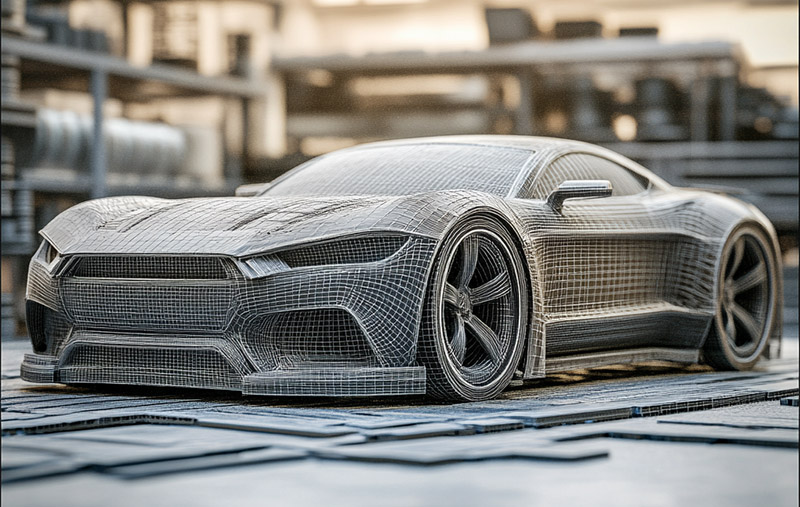
2. The key role of mold technology in new energy vehicles
The mold plays a crucial role as the basis for realizing the production of integrated structural components. It is a key tool for transforming design concepts into actual products, and its accuracy, complexity and performance directly affect the quality and production efficiency of integrated structural components. In the traditional automotive manufacturing model, chassis and body parts are processed separately, and the complexity of the mold is relatively low, but the production efficiency and quality consistency are also somewhat limited. The integrated design of new energy vehicles requires molds with higher precision and complexity to meet the molding requirements of different structural parts.
For example, for an integrated rear floor structural part, which has a complex shape and integrates the functions of several components, a mold is required to be able to accurately shape the various shapes and sizes. The design and manufacture of the mold must take into account factors such as the distribution of the wall thickness of the part, the setting of reinforcement bars and the way it is connected to other components to ensure the strength, stiffness and stability of the part.
At the same time, the selection of mold materials, heat treatment process and surface treatment technology also have an important impact on the performance and life of the mold. Suitable mould materials can withstand high temperatures, high pressure and frequent friction to ensure the precision and stability of the mold during long-term use. Heat treatment process and surface treatment technology can improve the hardness, wear resistance and corrosion resistance of the mold, extend the service life of the mold and reduce production costs.
3. Status of Mould Technology
(A) The application of advanced manufacturing technology
At present, 3D printing, CNC machining, rapid prototyping and other advanced mold technology are gradually applied to the production of key structural parts of new energy vehicles. 3D printing technology can directly manufacture complex shaped molds according to the design model without the need for the traditional mold processing process, greatly shortening the mold manufacturing cycle.
At the same time, 3D printing can achieve personalized customization to meet the special needs of different models and structural components. CNC machining technology has the characteristics of high precision and high stability, which can ensure that the machining accuracy of the mold reaches the micron level and guarantee the quality and performance of the mold. Rapid prototyping technology can produce mold prototypes in a short period, providing convenience for mold design verification and optimization.
(B) The integration of intelligent manufacturing and digital technology
The application of intelligent manufacturing and digital technology makes the mold design, manufacturing and maintenance process more efficient and controllable. Through digital modeling and simulation technology, engineers can simulate and optimize the design of the mold on the computer, predict in advance the problems that may occur in the production process of the mold, and make corresponding adjustments.
In the production process, intelligent production equipment can monitor the processing parameters in real-time to ensure the stability of processing quality. At the same time, digital technology also realizes the information management of the mold production process, improving the production efficiency and management level.
(C) Material and process innovation
In terms of mold materials, in order to meet the requirements of new energy vehicles on the mold of high strength, high abrasion resistance, and high corrosion resistance, new materials continue to be developed and applied. At the same time, the mold heat treatment process and surface treatment technology is also constantly innovating.
For example, carburizing, nitriding, nitrogen-carbon co-penetration and other surface strengthening treatment technologies, can improve the surface hardness and wear resistance of the mold, and extend the service life of the mold. In process parameter control, for the perfect optimization of the die casting process is also advancing. Die casting process, thermodynamic parameters and kinetic parameters and other settings directly affect the die-casting molding results, reasonable setting of these parameters can realize the optimization of die-casting results, effective control of die-casting molding quality.
Post time: Dec-06-2024