Калапот со инјектирање е широко користен производствен процес кој се користи за производство на различни пластични делови и производи.Овој разновиден и ефикасен процес овозможува масовно производство на сложени форми и сложени делови со висока прецизност и повторливост.Процесот на обликување со вбризгување се состои од неколку чекори, од кои секој е клучен за обезбедување на производство на висококвалитетни делови.Ајде да го истражиме процесот на обликување со инјектирање чекор по чекор.
Чекор 1: Дизајн на мувла за инјектирање
Првиот чекор во обликувањето со инјектирање е дизајнирање на калапот.Дизајнот на калапот мора да ги земе предвид факторите како што се аголот на нацртот, униформноста на дебелината на ѕидот, локациите на игличките на портата и ејекторот и поставувањето на каналот за ладење за да се обезбеди оптимален квалитет на делот и изработка.Дизајнот на калапот е критичен во одредувањето на димензионалната точност, завршната површина и структурниот интегритет на завршниот дел.Откако дизајнот на мувлата е финализиран, тој се произведува со прецизни процеси на обработка.
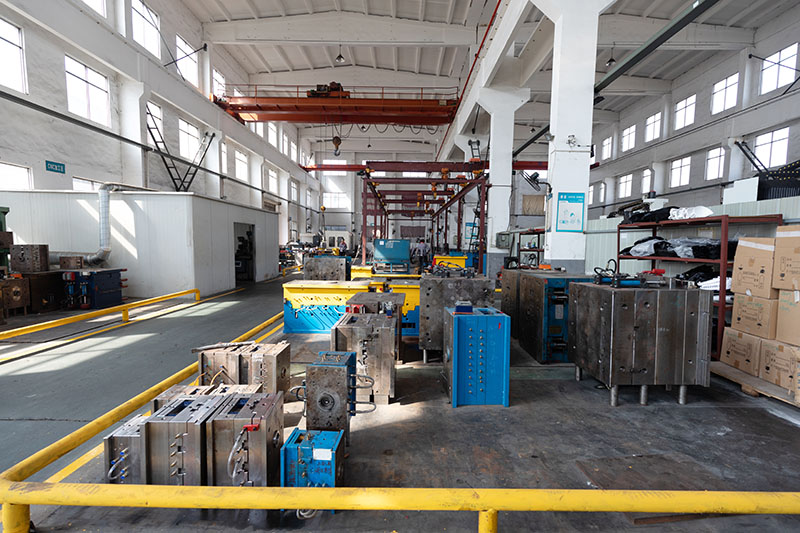
Чекор 2: Подготовка на материјалот
Суровините, обично во форма на пелети или гранули, се внимателно селектирани врз основа на специфичните барања на финалниот производ.Важно е да се земат предвид својствата на материјалот како што се протокот на топење, вискозноста, собирањето и јачината за да се обезбеди дека готовиот дел ги има саканите својства.Дополнително, бои, адитиви или зајакнувачки влакна може да се вградат во мешавината на материјали во оваа фаза за да се постигнат посакуваните перформанси и изглед.
Чекор 3: Стегање и инјектирање
Откако ќе се подготват материјалот и мувлата, започнуваат фазите на стегање и инјектирање на процесот.Двете половини од калапот се добро прицврстени во внатрешноста на машината за вбризгување за да формираат затворена празнина.Пластичната смола потоа се загрева до прецизна температура и се инјектира во калапот под висок притисок.Како што стопениот материјал ја пополнува шуплината, тој го добива обликот на конфигурацијата на мувлата.Фазата на инјектирање бара внимателна контрола на параметрите на процесот како што се брзината на вбризгување, притисокот и времето на ладење за да се избегнат дефекти како што се празнини, траги од мијалникот или искривување.
Чекор 4: Ладење и зацврстување
Откако ќе се пополни шуплината, стопената пластика може да се излади и да се зацврсти во калапот.Правилното ладење е од клучно значење за постигнување на потребните перформанси на делот и минимизирање на времето на циклусот.Дизајнот на калапот вклучува канали за ладење кои му помагаат на материјалот брзо и рамномерно да ја исфрла топлината, обезбедувајќи постојан квалитет на делови и стабилност на димензиите.Следењето и оптимизирањето на процесот на ладење е од клучно значење за да се спречат проблеми како што се деформација на дел или внатрешни напрегања кои можат да го загрозат интегритетот на готовиот производ.
Чекор 5: Исфрлање и делови
Отстранување Откако пластиката целосно ќе се излади и зацврсти, калапот се отвора и новоформираниот дел се исфрла од шуплината.Активирањето на игла за исфрлање или механизам вграден во калапот го турка делот надвор, ослободувајќи го од површината на алатот.Процесот на исфрлање мора внимателно да се разгледа за да се спречи оштетување на делот или мувлата, особено со сложени геометрии или делови со тенкоѕидни ѕидови.Може да се имплементираат автоматизирани системи за да се забрза исфрлањето и отстранувањето на деловите, помагајќи да се подобри севкупната ефикасност на производството.
Чекор 6: Намали и завршете
Откако ќе се исфрли делот, вишокот материјал (наречен брус) се отсекува или се отстранува од делот.Ова може да вклучува секундарни операции како што се бришење, отстранување на портата или кој било друг процес на завршна обработка потребен за да се постигнат спецификациите на конечниот дел.Се решаваат сите несовршености или недоследности на површината и во зависност од барањата за примена, делот може да добие дополнителна обработка, како што се обработка, заварување или монтажа.
Чекор 7: Контрола на квалитет и тестирање
Во текот на процесот на вбризгување, се спроведуваат мерки за контрола на квалитетот за да се обезбеди производство на висококвалитетни делови.Ова може да вклучува следење и контролирање на параметрите на процесот, проверка на деловите за дефекти и спроведување на различни тестови за да се процени точноста на димензиите, јачината и други својства.
Накратко, процесот на обликување со вбризгување е сложена и разновидна производствена технологија способна да произведе широк спектар на пластични делови и производи со исклучителна прецизност и ефикасност.Секој чекор во процесот, од подготовка на материјал и дизајн на мувла до ладење, исфрлање и контрола на квалитетот, бара внимателно внимание на деталите и експертиза за да се постигнат оптимални резултати.Со разбирање и оптимизирање на секоја фаза од процесот на обликување со вбризгување, производителите можат постојано да испорачуваат висококвалитетни, економични делови за да ги задоволат потребите на различните индустрии и апликации.
Време на објавување: Декември-12-2023 година