射出成形は、さまざまなプラスチック部品や製品の製造に広く使用されている製造プロセスです。この多用途かつ効率的なプロセスにより、複雑な形状や複雑な部品を高い精度と再現性で大量生産することが可能になります。射出成形プロセスはいくつかのステップで構成されており、各ステップは高品質の部品の製造を保証するために重要です。射出成形プロセスを段階的に見てみましょう。
ステップ 1: 射出成形金型の設計
射出成形の最初のステップは金型の設計です。金型の設計では、最適な部品の品質と製造性を確保するために、抜き勾配、肉厚の均一性、ゲートとエジェクター ピンの位置、冷却チャネルの配置などの要素を考慮する必要があります。金型の設計は、最終部品の寸法精度、表面仕上げ、構造の完全性を決定する上で非常に重要です。金型の設計が完了したら、精密機械加工プロセスを使用して製造されます。
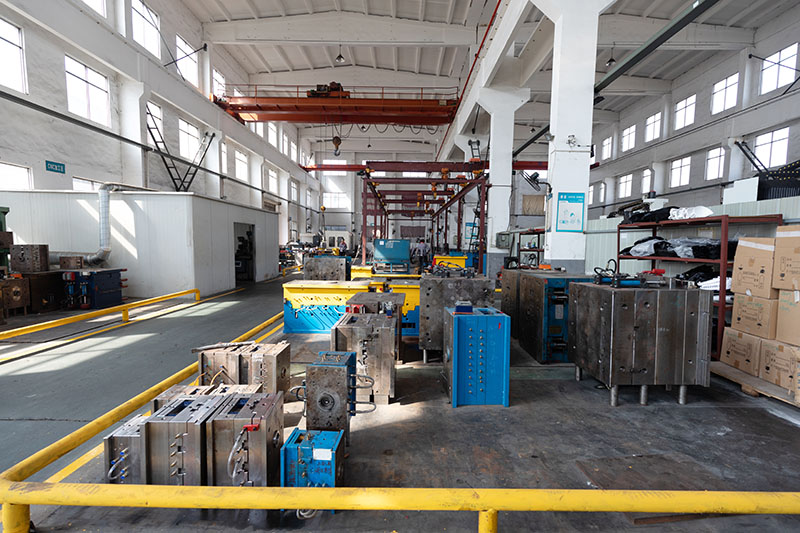
ステップ 2: 材料の準備
通常、ペレットまたは顆粒の形の原材料は、最終製品の特定の要件に基づいて慎重に選択されます。完成した部品が望ましい特性を持つようにするには、メルトフロー、粘度、収縮、強度などの材料特性を考慮することが重要です。さらに、所望の性能と外観を達成するために、この段階で着色剤、添加剤、または強化繊維を材料ブレンドに組み込むことができます。
ステップ 3: クランプと射出
材料と金型が準備されると、プロセスの型締めと射出の段階が始まります。金型の 2 つの半分は射出成形機内でしっかりとクランプされ、閉じたキャビティを形成します。次に、プラスチック樹脂を正確な温度まで加熱し、高圧下で金型に射出します。溶融した材料がキャビティを満たすと、金型構成の形状になります。射出段階では、ボイド、ヒケ、反りなどの欠陥を回避するために、射出速度、圧力、冷却時間などのプロセス パラメーターを注意深く制御する必要があります。
ステップ4:冷却固化
キャビティが満たされると、溶融プラスチックは金型内で冷えて固化します。適切な冷却は、必要な部品の性能を達成し、サイクル時間を最小限に抑えるために重要です。金型の設計には、材料の熱を迅速かつ均一に放散させる冷却チャネルが組み込まれており、一貫した部品の品質と寸法安定性を確保します。冷却プロセスの監視と最適化は、完成品の完全性を損なう可能性のある部品の変形や内部応力などの問題を防ぐために重要です。
ステップ 5: 取り出しと部品
取り外し プラスチックが完全に冷えて固まった後、金型が開かれ、新しく形成された部品がキャビティから取り出されます。金型に組み込まれたエジェクタ ピンまたは機構を作動させると、部品が押し出され、工具表面から解放されます。特に複雑な形状や薄肉の部品の場合、部品や金型への損傷を防ぐために、突き出しプロセスを慎重に検討する必要があります。自動化システムを導入すると、部品の取り出しと取り外しが高速化され、全体的な生産効率の向上に役立ちます。
ステップ6: トリムと仕上げ
パーツが取り出されたら、余分な材料 (バリと呼ばれる) がパーツからトリミングまたは除去されます。これには、バリ取り、ゲート除去、または最終部品の仕様を達成するために必要なその他の仕上げプロセスなどの二次作業が含まれる場合があります。表面の欠陥や不一致はすべて対処され、用途の要件に応じて、部品に機械加工、溶接、組み立てなどの追加の処理が行われる場合があります。
ステップ 7: 品質管理とテスト
射出成形プロセス全体を通じて、高品質の部品の生産を保証するための品質管理措置が導入されています。これには、プロセスパラメータの監視と制御、部品の欠陥検査、寸法精度、強度、その他の特性を評価するためのさまざまなテストの実施が含まれる場合があります。
要約すると、射出成形プロセスは、非常に高い精度と効率で幅広いプラスチック部品や製品を製造できる複雑で多用途な製造技術です。最適な結果を得るには、材料の準備や金型の設計から冷却、取り出し、品質管理に至るプロセスの各ステップで、細部への細心の注意と専門知識が必要です。射出成形プロセスのあらゆる段階を理解して最適化することで、メーカーは、さまざまな業界や用途のニーズを満たす高品質でコスト効率の高い部品を一貫して提供できます。
投稿日時: 2023 年 12 月 12 日